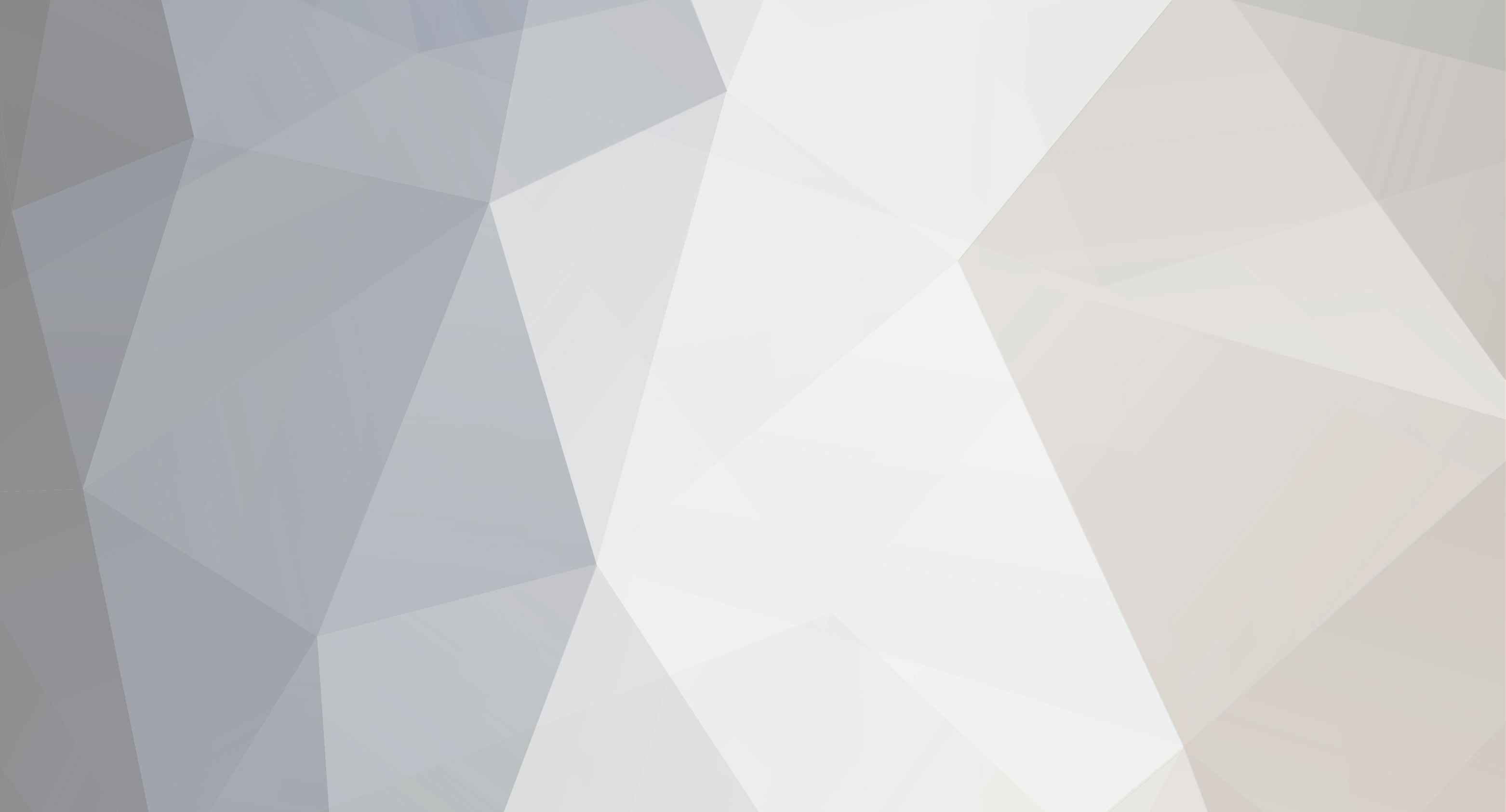

outhopu
Members-
Content Count
329 -
Joined
-
Last visited
-
Days Won
4
Content Type
Profiles
Forums
Gallery
Everything posted by outhopu
-
High Ouput Alts
outhopu replied to Deto1992's topic in Amplifiers / Head Units / Processors / Electrical
Nice link. Lots of good info in it. -
A Suburban A Warhorse and a pair of Double Dees
outhopu replied to onebadmonte's topic in Build Logs
It looks like it belongs there. I like it a lot. It's not going to be fun drilling all those holes though. I always hate having to drill holes when laying under neath a car. Do you plan on putting a plate in the bottom of the tray to protect the battery cases from anything that might get tossed up from the road? -
The nice thing is at least with it having hydraulics it can be raised up to display a lot of the work still. I like the swoopy lines myself but anything that has to be straight I'm trying to make nice and crisp. All the corners will be rounded over after it comes back from the blasters after mock up. Other side close to finished. Also got the top of the arches done. I'll wait to get the last few imperfections worked out until after all fab work is done and the frame comes back from being shot blasted. I'm just pushing ahead with grinding. I was able to remove the frame from the jig since all the plates are now welded. It's nice not having all the braces in the way now. Getting the lower side polished down.
-
A Suburban A Warhorse and a pair of Double Dees
outhopu replied to onebadmonte's topic in Build Logs
Running gas just makes it easier to since there isn't as much smoke and you get a better view of whats going on. I wasn't knocking your welds, just your welder a little bit. -
A Suburban A Warhorse and a pair of Double Dees
outhopu replied to onebadmonte's topic in Build Logs
Brackets truned out real nice. I wish I had access to a CNC machine for doing my plasma cuts as well. I've got nice plasma cutter but I just don't have as steady of a hand as I once did so I always end up having to sand the edge smooth. Does your 110v welder have a hook up for running argon? Getting away from using the fluxcore wire will do wonders for the apperance and cleanlyness of your welds. It looks pretty respectable for what your working with. -
While I'm waiting on a couple parts I've been grinding rewelding and grinding some more. Everything is getting this level of finish. This section won't even been seen once the body is on.
-
Dude invest in a decent router with a plunge cut base and get a circle jig. I put off buying a router for 15 years for some dumb reason and the first time I used one with a circle jig I could have kicked myself for not getting one earlier. You should be able to get a decent router, circle jig, and some bits for rounding over edges for $200 or less. I've always invested in metal working tools and finally picked a few decent wood working tools up and it made a huge difference in the quality of my work. Looking good by the way. I did laugh a little at the cutting in the house but hey what ever it takes to get the job done.
-
Builder handled the motor once we pulled it. Problem with the cam, ate a couple of lifters. I think it was a bad grind, but can't say I never saw it before or after. Grasshopper figured since it needed a new cam he would put in a roller cam. Zinc in the motor oil today is partly to blame, (the lack of it) Also when starting a motor with a flat tappet for the first time it should be run around 2000 2500 rpm for the first 30 minutes with Break-In Oil Additive. but with a roller cam no such problems That's why we were pretty blown away about this situation, because we added zinc and ran a breakin of 30 minutes @ 2200rpm. Oil pressure looked ggod the whole time, it wasn't till the next day or so and the oil pressure had dropped. Like you said, with the roller it is a done deal. Thanks for the post! First time I looked in on this build. No surprise on the quality. You guys are kicking as on this one. The cam issue seems to be becoming an all to common problem these days. In the last few years I've had at least 3 different guys do motor rebuilds and wond up with the cam being eaten up. They all did proper break in with the "good" break in oil that has the added zinc also. I won't do anything besides a roller from here out, todays cams are straight garbage and need all the help you can give them to hold up.
-
Haven't checked in this build in a while. It really came together nicely. This is a perfect example of the importance of doing the job right. Even if this type of car isn't somebodys cup of tea there is still plenty to appreciate in this build. I wish I could have got my old man to put time in with me in the garage when I was young like you have.
-
I'm not even keeping track. If I counted the hours I'd just get overwhelmed and give up. It's going to be into the thousands of hours by the time it sees the road again. Thanks again as always.
-
Way to man up and start cutting. Off to a good start and looks like you have a good selection of tools to do the job properly.
-
Got most of the 1st round of welding done on the frame today. I even welded all the lower corners. I want to do as much of the welding as I can while the frame is locked down on the jig. Also welded the housing ends on the rearend. I full welded the inside for now. I'm holding off on doing the outside, I may take it to my friends shop and use his tig welder for the outside weld. Then I started polishing down some weld. This section is ready to be rounded over. This section will need some more weld first. It's a little hard to tell but the white looking areas are low spots. Basically I will end up grinding all the welds down then going back over everything again with another bead of weld to build the shoulder up then grind it all a second time to get the perfect squared corner. After I get the entire frame to that point I'll round all the corners over. The corners have got to be smooth and straight without any bondo.
-
A Suburban A Warhorse and a pair of Double Dees
outhopu replied to onebadmonte's topic in Build Logs
Thats why I do detailed builds. I love seeing quality work and if my builds assist in that for somebody else then it's all worth it in the end. -
Thanks guys but at the rate I'm going it will be years and not year. Lol. Work has been hit and miss for a while now so this and other projects have kept me busy in my down time. I'm not one to sit around so I just make sure there is always something in the garage to work on to keep me from going crazy. I work as many hours of the day as possible some times it's only a couple hours some times it's 14 hours. I'm a single father also and I make sure to spend a fair amount of time with my daughter. Before I had her I'd work almost everyday of the year 12-18 hours a day, I spent many of holidays in the garage in my younger years.
-
Well it's good to hear they will still work for IB car audio application. I'm sure there is a very small market for IB car audio but when done properly the results are amazing. Lots of trunk space, less watts needed, less electrical upgrades, weight savings, lower cost...makes me wonder why the market isn't bigger. Keep up the good work I love your products.
-
I'm not into home audio stuff but every home stereo I've ever owned used 8 ohm speakers so thats one thing that stands out as a problem for car audio application. If they end up being the exact same sub with a different name that doesn't bother me, I just need to know it will still perform the same as the ones I have now. I'm just sick of everything I like going away or changing for the worse. IB car audio may seem odd to you but you have a trunk with room to spare. The cars I build have very little to no trunk space so it's the best option for me. Thanks. That was the first car I used them in and was blown away by the performance. It's a proper IB set up and the subs have seen 15 hz notes without any problems. It was just sounding like they weren't going to be exactly the same product.
-
This pisses me off big time. The IB3 line was what made it possible for me to put some serious bass in a car that would not have room for a conventional ported sub box. Here is a pic and a few videos of the Caddy I'm working on. It's getting a trunk full of hydraulics and batteries and the IB3s saved the day for us. This sub should not be pulled from the car audio line up. 4 12" IB3s powered by a Sundown 2000d @1 ohm.
-
Thanks. Bored all the body mount openings out. They are the exact size as the original opening so the body mount will sit on the reinforment plate instead of the stock frame. I'll trade the body sitting 3/16" of an inch higher for the gain in strength. I had to make an adapter for the tube adapter since I'm not using round tube. I plug welded all 4 side and welded each end of the tube to insure it will hold up. Made a mock up arm to check out how the geometery is going to work with all the mods. Once I determine the final length and shape needed for the upper arms I'll do the real arms. Just grabbed some scrap pieces out of the pile that were close to the shape needed. I know the spindle is for the other side but it served it's purpose for now. I'm waiting on the tapered reams until they get here I can't go any further.
-
A Suburban A Warhorse and a pair of Double Dees
outhopu replied to onebadmonte's topic in Build Logs
Yeah, better safe than sorry. My friend is a pretty good welder, he does chassis work on race cars and stuff. Maybe one day when I grow up I'll be able to lay down a fat bead like you. It just takes practice and technique, you'll get there. You fit all the pieces together properly for a strong weld thats just as important. Doing the corners the way you did is the strongest way to joint 2 pieces of angle together because it gives you the largest weld surface. This should be a nice install when it's all said and done. -
A Suburban A Warhorse and a pair of Double Dees
outhopu replied to onebadmonte's topic in Build Logs
I like the little overlap trick you used there to get the drivers to fit. Everything is looking good overall. Good call on having the rack welded for you if your not completely confident it your welding ability, that is a lot of weight (and money) it will be holding. -
No pics of the box carnage? I always like to see how things fail so I can better understand how to prevent it. Good looking build that sucks about the box.
-
Looking real clean so far. Keep up the good work.
-
Made the other plate for the side. Also tied the plate into the tubing where possible for more strength. Polished the edge of the balljoint sleeve where the plates came together.
-
No truss on the axle. Using semi float stock style 9" axles from Dutchman. They only case harden their axles which gives them more strength without making them brittle. I've bent 1 5/8x1/4" wall with my JD2 but it required an extra long handle for leverage. I have changed my mind on doing the tubular arms anyways though so I won't need to use the bender on this. Got started on a lower A arm today. The coil pocket has been relocated for better alignment with the cylinder and the pocket has been dropped 1" also. I used some 1 1/2x1 1/2x3/16" and some 1x3x1/8" to make a skeleton to hold everything in it's place and add strength. Made sure all the pieces were coped for a tight fit and strong weld. I'm using 1/4" plate for the side plates. The coil bucket will get trimmed down after I cap the top. The tube is welded to the joint sleeve and then the plate is welded to the sleeve on the outside and tied into the tubing also for maximum strength.
-
Got the other end to line up and tacked it on. Also verified that the ends and alignment bar were square. It's now ready for full welding and rear suspension mock up. My friend got my ball joint sleeves machined for the lowers.