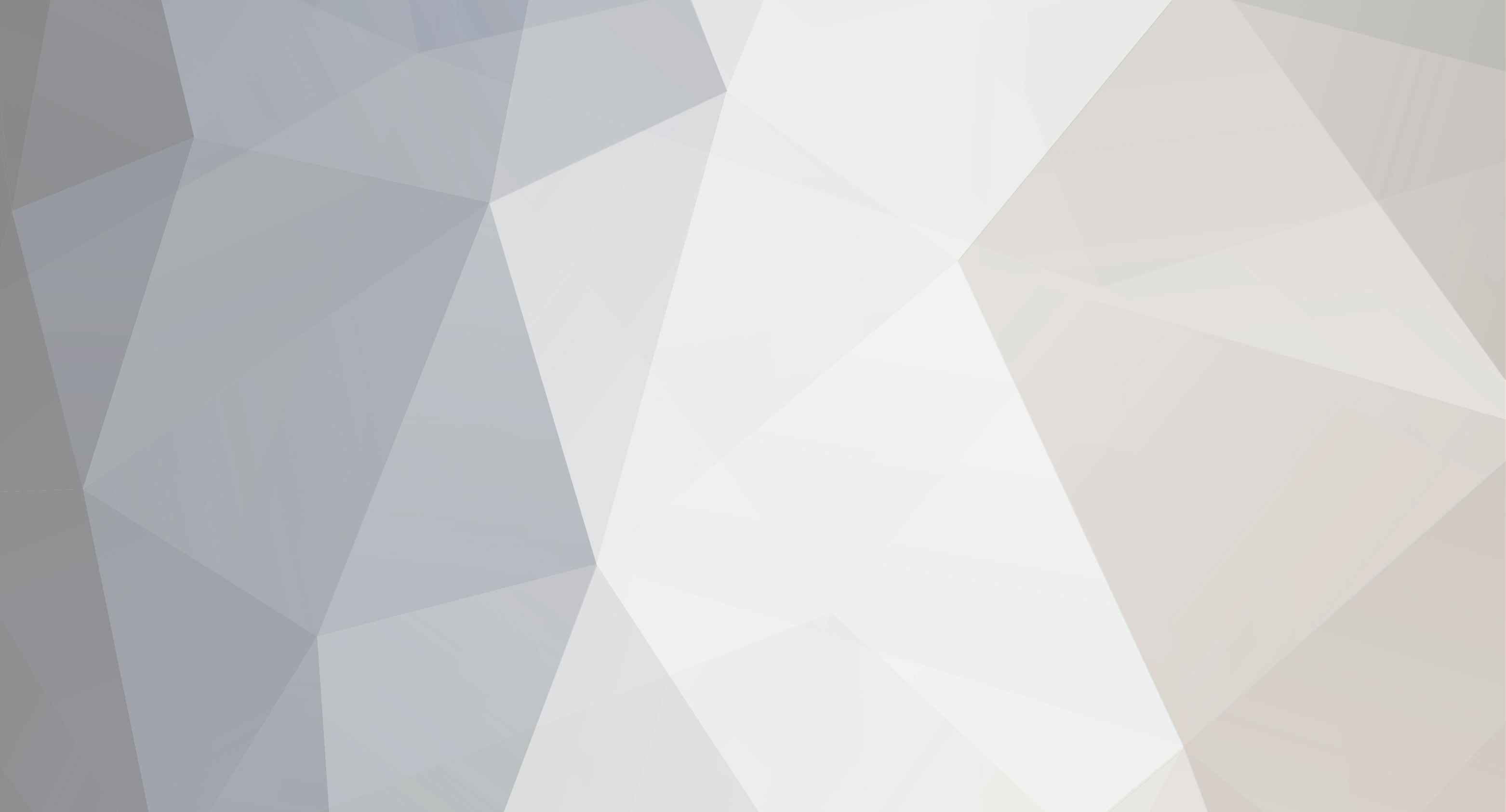

outhopu
Members-
Content Count
329 -
Joined
-
Last visited
-
Days Won
4
Content Type
Profiles
Forums
Gallery
Everything posted by outhopu
-
No, but I plan on using the same suede material that I used on the sub baffle when I'm done with them. When you think you'll be done with them? I don't know for sure. I'm busy as hell with building another lowrider that needs to be finished by the end of next month. So for now I'm just working on the Caddy here and there. Here is a link to the other ride I'm doing. Check the build up and you'll see why I'm not done with the Caddy yet. LayItLow.com Forums -> G-Body frame wrap I'm working on..
-
He hasn't had to do anything other than oil changes since he bought it. Thing is still like new, low miles, and well cared for.
-
Coming together nicely. Thanks for doing the video on the 2 different alternators. I've been trying to find good info and your video was exactly what I was looking for.
-
No, but I plan on using the same suede material that I used on the sub baffle when I'm done with them.
-
I got a little more done last night.
-
I had these in one of my old rides and really liked them. They handle lots of power and get loud as hell, without straining and distorting. Yes they are very detailed and clear even if given dirty power it is hard to get them to distort but they will if you push them hard enough. A lot of people sleep on these speakers, if I ever go passive again it will be strictly Infinity. I was running them off a RF 4 channel amp pushing over 100w rms to them and they took it no problem. I've heard other speakers that cost way more that didn't perform as good.
-
I had these in one of my old rides and really liked them. They handle lots of power and get loud as hell, without straining and distorting.
-
Well like I said before I wasn't really happy with the doors so I started to rework the drivers door today. Made a new panel with a recessed area to allow the speaker plate to be angle mounted . I used 1/4" hardboard for the under layer then 3/4" MDF for the trim piece to do a semi flushed grill. Glued it together and did a mock up of it. May change the angle a little. Used some body filler to flush the lower half of the grill into the board. Still needs another layer of filler and more sanding. I'm much happier with the way the speakers are looking now.
-
It's called plum but looks really purple in the pics. It's a good match to the interior though so I'm happy with it. I don't think the undercoating will pose any other issues now that I'm done handling and moving it around. The shit just scrapes off way to easy. Worst part about it is I was going to buy some spray cans of bedliner but figured the undercoating would work. Now I know.
-
Well I had a couple of hours to spare today so I wrapped the baffle board and installed it. I still need to seal it up with foam but it's at least in the car now. All the holes are for the subs bolts and trim piece bolts. They get covered by the trim. I still need to attach and paint the side trim pieces. By the way if anyone was considering using the undercoat method I did, DON'T! The dam undercoating doesn't stick for shit to the wood and I had some peel off on me when I taped the painted section off to keep the spray glue off it. I touched it up but I was super pissed off about it. Oh well live and learn.
-
4 Fi Audio IB3 18's walled off 15Hz tune in a VAN BUILD LOG
outhopu replied to kryptonitewhite's topic in Build Logs
Thanks man. I'm lucky and have a fiberglass/composite supply shop 2 blocks away from me. I really like the stuff. It sets in a matter of minutes and is very solid yet easy to trim and sand. It is pricey though. Here is a random link I found for referance Urethane Foam , Expanding Marine Polyurethane Foam -
4 Fi Audio IB3 18's walled off 15Hz tune in a VAN BUILD LOG
outhopu replied to kryptonitewhite's topic in Build Logs
Have you ever tried using the 2 part expanding foam that has an A and B you mix together? That stuff cures much more evenly and doesn't require air since it's a chemical reaction. It can also be used for doing speaker pods. It allows you to shape the foam then cover it with fiberglass. It's just so much easier to work with then doing the wood and bondo method. Here is a link to a truck I did that I used some 2 part foam on the door pods. Just to give you an idea of what I'm talking about. F150 Lightning build up. - SSA Car Audio Forum Your off to a good start. Just figured I'd share whats worked for me to save time and labor. -
Step up to a machine that uses gas and you'll be in love. I put off buying a good mig machine for years, due to cost. Once I finally did it I was pissed at myself for using my old arc machine for so long. I think you may be right. Time will tell. It will be a bit though. I'm working on multiple projects and had to get back on another one to finish it up.
-
110v w/gas are nice for doing sheetmetal but thats about all I use them for. I recently upgraded from a Miller DVI unit that would run on 110v or 220v to a 220v Miller 252. The old DVI unit worked great up to 3/16" but the 252 blows it away for doing thicker material.
-
It's really important to me that I make the entire install look top notch. My boy and I have wanted to do a system that looks and sounds good for way to long. We've always managed to get something "temporary" that sounds good but always looked like hell. I'm tight on time but I'm trying to make sure it gets done proper. Mig w/gas is the only way to go. I do a lot of welding and fab work and couldn't do what I do without a proper machine. I'm also an overkill kind of guy so yes safety is a must.
-
Glad you all are enjoying the build. I managed to get a couple coats of semi gloss black over the undercoating today. I'm pretty happy with the texture, it saved me a lot of sanding for sure. I'll give this a couple days to fully cure before attempting to wrap it.
-
Thanks for the rating. I didn't know what the stars were about, now I do. I know what you mean. It looked good even with it just being bare MDF, then I wrapped the bezel and I really felt like it was coming together. I'll be doing a full report on the performance of everything when I get it up and running. The car had 4 10" Kicker comps in a sealed box before running off 900 watts so I have something to compare the IB3's to. I'm confident they should way outperform those.
-
You could add some more bracing to the door if you have a big enough opening to get it in there. There are panel glues out there that are strong enough that they use them to glue door hinges on. A good autobody supply place should be able to help you select the right one. Then you could bond a piece of steel tubing to the skin. A piece long enough to tie into the front and rear of the door frame would be ideal but may not be practical to fit into the door. Just an idea I've been kicking around for something I'm working on.
-
I like to post my work for others to enjoy. I feel like I still have a ton to master and being able to see how others do it gives me insite. Thats why I post lots of pics and give details to help do the same for the next guy. I got started on spraying the back and decided to do the center of the front in case the suede doesn't work out going around all the curves and corners. I'm starting with undercoating to give it a textured finish and to hide the sand scratches. I'll be spraying a coat of semi-gloss black over it for a better finish. None of the bare ares will show once installed.
-
I was amazed when I finished it without any wrinkles. I just took my time and it all came together.
-
I found some bootleg suede that is almost a perfect match to the headliner and rear pillar material. So I decided to give it a try. I started with the trim bezel for the subs since it seemed like it was going to give me the most headaches. First I had to sort out how to fasten the bezel before covering it. I used T nuts again with a recessed pocket via the router. Then used filler over them. I taped over them to keep filler from getting in the threads. I'm going to just use a few screws at the ends since the wood is too thin to use the T nuts. Filler sanded and ready to be covered. This was not easy to get it all to lay down smooth and wrinkle free with all the curves and routered edges. It came out real nice though. Especially considering I've never really done it before. Nice and smooth even on the round ends. I'm thinking I'll do the same to the face and top and just do a textured paint on the back side.
-
I'm going to do a lot of work on the body to keep flex and rattles to a minimum. Thanks again fellas.
-
I welded the last pieces of the bracing in tonight. These tabs ties all the bracing and baffle board together None of the sheetmetal bears any load of the subs now. Plus the baffle board being bolted in will give strength to the beltline of the body again. Now to decide how I want to cover the MDF. Thanks for all the positive responce. I'm busting ass on this thing so the pics will keep coming for now.
-
I test fit the rear seat back before removing the baffle board. Fits nice, the seat still sits higher than the board. Installed T nuts for subs and bolted the brackets on. Used T nuts on the bracket mounts also. I recessed the area with the router and cut the bolts flush so I can cover them with filler. Started with the filler. Did some more bracing while the filler was setting up. More 2x2x3/16" angle with a 3x4x3/16" foot. The foot rests on the boxed section of the body for strength. Just have a couple small tabs to weld on and the bracing is done, then onto finishing the board.