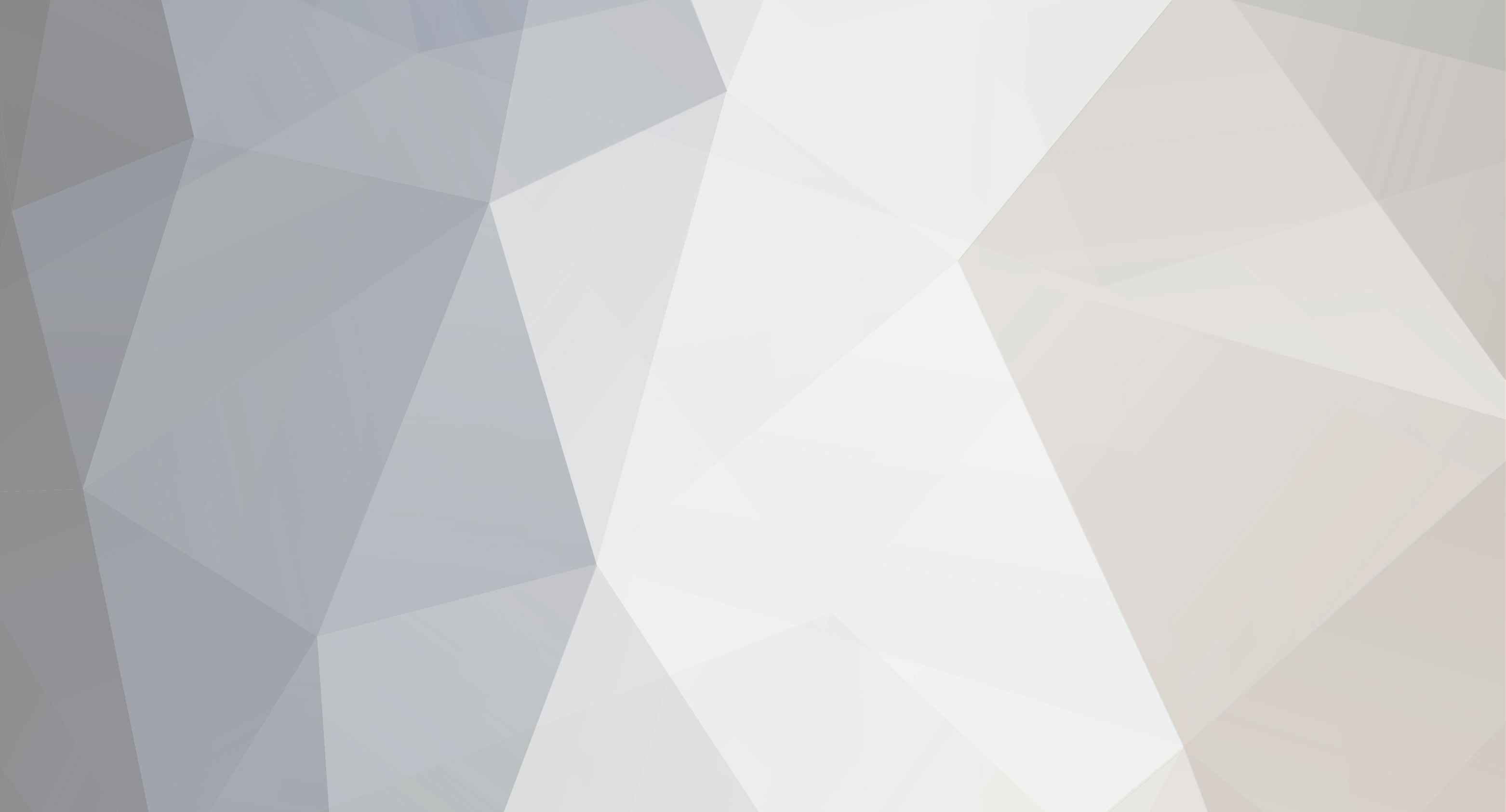

Totalnewbie007
Members-
Content Count
175 -
Joined
-
Last visited
Community Reputation
-4 A few mistakesAbout Totalnewbie007

-
Rank
Member
-
*nothing*
-
*HELP* Troubleshooting SAZ-3000D that after sitting has started going
Totalnewbie007 replied to Totalnewbie007's topic in Sundown Audio
I ohmed all the mosfets; on the power I got 15+ meg ohms, and I had 28k+ ohms on all the output transistors -
*HELP* Troubleshooting SAZ-3000D that after sitting has started going
Totalnewbie007 replied to Totalnewbie007's topic in Sundown Audio
-
*HELP* Troubleshooting SAZ-3000D that after sitting has started going
Totalnewbie007 replied to Totalnewbie007's topic in Sundown Audio
I did some testing; I have a 12v powersupply thanks to a optima d31a; 1125 cranking amps; 900 cold; 75 amp hour battery just sitting around... I did millivolt testing From the positive terminal; I can measure hundredths of a millivolt; I got ~29mv on exposed windings closest to the power in. ~5mv on each heat sink. marked in green I have 102 volts. Any ideas where to start; can someone help me trace the protection circuit? -
*HELP* Troubleshooting SAZ-3000D that after sitting has started going
Totalnewbie007 posted a topic in Sundown Audio
unfortunately, after re-installing my car audio I found my sundown amp going into protect. It goes into protect immediately; the power light turns on about 1-2 secs later; 5 seconds later the two relays marked with a purple X close/open(click)...; unhooked from speaker; I found manufacture damages that were covered in glue, marked in black; red. In pink there is some rubbing damage to the winding; no metal caps blown; the plastic ones which the top may have some give; each one can depress at-least a mm or so. That's all I can tell visually. I cannot smell burnt electronics; nor are any burns prevalent on top of the board. I've built small circuits and studied them a lot; and have a megger which probably wont be needed; along with a 400mfd/~2Mohm range; and MV Meter... I also have an oscilloscope. So please help get me to a starting ground on repairing this amp; I have good soldering skills. And can re-paste the transistors tot he heat sink with high quality thermal compound. Pictures are large for detail... yellow rub; black manufacture damage yellow rub; black manufacture damage all manufacture damage; have glue over it; yellow insulation missing on wire; black minor heat shrink overheated. X's represent relays turn on/of after 5 seconds. In yellow rub; pink manufacture damage -
Painted with silicone
-
Ok well I got to cut the ports; then it rained and lightninged, so I went inside. I got back out and went ahead and painted it with the same silicone I had before. I figure it will seal better when I put the cover on. The ports are 15.5 inches; changed the peak; but I have enough room for some elbows which should give me 6-7" longer port; still a cry from the 30" planned, but we'll see what happens. I'm going to test it sealed first; then bandpass w/ 15.5" ports; then with ~21-22" ports; and so on. Legend: Red is the 30" port Orange is the 22" port Yellow is the 15.5" port Green is a 6.83 Cubic Ft sealed box It was a tight fit!
-
Ok well I'm going to cut the ports and put elbows on them! Just wanted to make that clear; However 6" elbows are harder to come by than I thought; so I'm gonna visit a sewer guy I know or order them online. Today I'm going to wire the amps and cut the ports; going to leave it sealed. I've found out that my engine battery (a kinetik 6800?) went bad; doesn't charge. Using a Optima d3100? as a start battery; then disconnect it; engine runs without; tried charging it at 2k rpms for 20 min; but unless it's totally dead; it wont even put the windows down or unlock the doors. On to the {PICS!}
-
Look ma no screws! I love my corner clamps for sure; I also love clean even cuts; very few gaps. I line up my clamps; test fit; rub my finger at the seems and adjust the clamps till I don't feel any edges; tighten one side of the corner clamps; raise the board; brush glue; drop; clamp corners; add big clamps near corners and tighten each back and forth; add center clamp and tighten; then finish cranking all three down till the glue completely fills the voids.
-
Ok well the sheets got cut today; I had to clean the porch to work to mess it up again. However with a skill saw I still manage to get cuts within 1/8th of an inch; My method of measuring is meticulous I use the factory cut edges of the boards in order to setup a guide. I lined the corners up flush to the guide; the cut board; and the support directly on the chairs I used as saw horses. From there I do the following: Measure the saw blade to the rim of the saw to determine the distance of the blade to the guide depending on which side of the board I'm on (I account of the thickness of the blade) Basically if I'm cutting from the 4x8 sheet and the guide is on the outside the cut. I need to factor in the thickness of the blade plus the distance to the guide from the rim of the saw. If the guide is sitting on the board and I'm trimming it to size; I factor out the blade and just use the distance of the blade to rim. I make two markings on the cut sheet the guide arrows and cut arrows using a tape measure. I place the guide down and line the board on the center of the arrows and clamp down. Here is the tedious part: I use a block to nudge the board into alignment before while and after clamping it in place; Then I cut a test notch; measure my board; adjust if necessary; then rip it in a few seconds maintaining and even level pressure perpendicular to the cut. Spend 10-20 minutes measuring; and a few seconds cutting. I speed things up as I get going I will assembly with minimal screws tomorrow. I've already figured how the box is going in; I will have to take off my passenger door to do it; along with the seats out. I will have some more interesting pics tomorrow. The guide is on the outside of the cut here. To keep the saw from binding, the support is at the guide; this will pull the board away from my blade to keep it from pinching; another chair that is slightly smaller is there to keep it from bending too far and from falling. Here is a picture of the test cut and measurement; This one was spot on at 34" Note the guide was on the inside of the cut here; the blade is on the outside; distance of the blade to the rim was 1 1/8th inch plus 32 and 7/8" (the guide position) Thanks for looking
-
Got the car cleaned and painted with silicon to act as a sound deadner...took 4.5 hours. THE MESS! I sat there and vac'd every square in and it still looks dirty as hell One thorough coat applied in the skipped trunk and through out the car.
-
I'll wait for these components. I hope I can get these around march next year.
-
ok well I'll let you know how the bandpass goes this week
-
http://www.bcae1.com/#116 Qtc Qtc is the total Q of the speaker in an enclosure including all system resistances. A Qtc of .707 is the most common and generally produces the flattest frequency response with approximately a 6dB/octave rolloff. Higher values of Qtc will give a peak in the output with a sharper rolloff. A lower Qtc will start to roll off earlier and will roll off at a slower rate. If you don't know what Qtc you need, start with a Qtc of .707. Qts Qts is the total Q of the speaker. It is defined as 1/Qts = 1/Qes + 1/Qms.
-
Do you know anything about this sucker, all I can tell is it will probably do best in a sealed enclosure.